Foundry Activities – For GEORG FISCHER GMBH in Mettmann “standstill means a setback”. Process optimisation focused on improving blasting materials handling
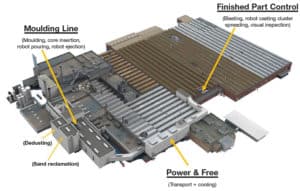
In foundry processes overall cleanness of castings is of pivotal importance for the downstream inspection, treatment and other process steps. The use of predominantly abrasive blasting materials, which can vary widely in shape and properties, constitutes a particular challenge for returning materials by means of conveying installations.
This has now been optimised by GEORG FISCHER in Mettmann (Germany). In 2012 one of the world’s most modern manufacturing plants for the resource-saving production of lightweight components for the automotive industry was commissioned.
One of GF Automotive’s biggest iron foundries took 13 months to build and investment costs amounting to approximately EUR 36 m. The production line called Aeration Moulding Robotpouring (AMR) follows the trend towards lightweight construction. The new line with a capacity of up to 60,000 tons of ductile iron castings – the total production capacity at Mettmann amounts to 200,000 tons – is suitable for producing especially filigree and, hence, lightweight castings.

At the Mettmann site GEORG FISCHER Automotive manufactures chassis components, rear axle covers and crankshafts for passenger cars and commercial vehicles, to name but a few parts. Lightweight components made by GEORG FISCHER are used in the new Audi A3 or VW Golf, for instance. They bring weight reductions of over 25% compared to conventional components.
After approx. 4 years’ operation of the blasting system in the production-control section, the company decided to optimise the screening and return of the blasting material with two vibratory trough conveyors The project was headed by Ralf Leiffels (Head of Machine Technology at Georg Fischer GmbH).
“Over the entire operating cycle of the vibratory trough conveyors, which were connected in parallel and which had been delivered by another manufacturer together with the blasting unit, the failure of vibration drives, cracks forming in side walls and drive cabinet as well as unintended blasting material leakages caused an increased number of unplanned downtimes. The multitude of minor and major failures of the handling system located in the basement and therefore located in the segment of production not permanently visible, made our trust in this technology dwindle,” says Ralf Leiffels in hindsight and adds: “Therefore we contacted CYRUS and first analysed the situation on site. The response speed and the high-quality solution worked out in a short period of time convinced us to go with CYRUS for this modernisation.”
The vibratory trough conveyor primarily serves to separate the impurities from the blasting material. This is achieved through two screening stages (Illus. 4).
The technical optimisation proposed by CYRUS among other things includes a vibration monitoring control unit of the vibration drives. This control generates an error message in the event of a failure and turns down the drives in a controlled process. The vibration data is monitored by an evaluation unit also supplied by CYRUS.
“This proved to be a viable preventive measure in many other foundry applications in order to prevent damage caused to the system,” says Holger Ververs, Head of Design and Applications Technology at Cyrus GmbH Schwingtechnik.
Furthermore, a sandwich bottom –consisting of a trough bottom, rubber layer and wear sheets – was used in the area of the blasting materials reception so as to minimise noise emissions. Long service life is ensured by wear sheets made of HARDOX 450. These guarantee high wear resistance, on the one hand, and permit the processing of cold bent parts. The special design of the screw fastening makes for quick replacement in the event of wear.
For the screening function
CYRUS has provided main screening with a mesh size of 5mm x 5mm. The second downstream screening area serves as an additional safety feature ensuring foreign bodies are separated as these may only appear at the end of the approx. 4m-long screen deck. To cater to the use of various blasting materials, a quick-change option for screen linings is provided.
“We are very satisfied with the way CYRUS executed and implemented the modifications. We are convinced that the new conveying technology will make an important contribution to the operational excellence of our new manufacturing line in future,” says Ralf Leiffels.
Technical Parameters:
Scope of delivery: Two CYRUS
SRU 1000×6300-QS-SE-A-AM vibratory trough conveyors
Throughput: 200 t/h
Piled density: 4.35-4.55 t/m³
No. of screen decks: 2
Cover: Yes
Bearing: Rubber-coated hollow springs
Drive: Imbalance
Rpm: 980 min-1